Hyodong Machine Breaks World Record with the Arrival of HBP-6220UL Super-Large Bolt Part Former!
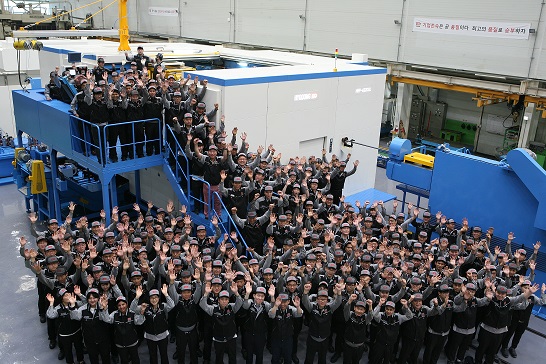
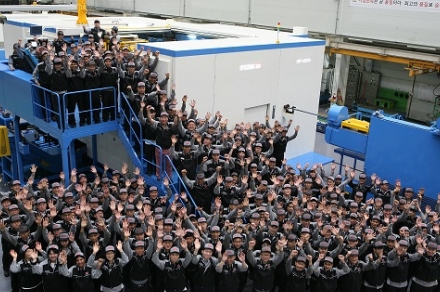
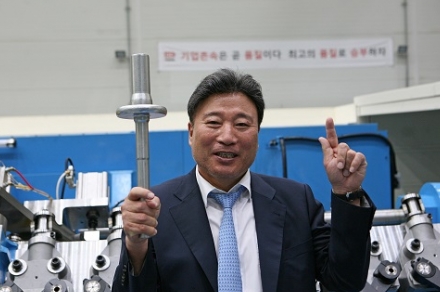
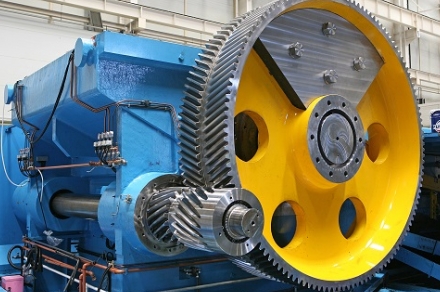
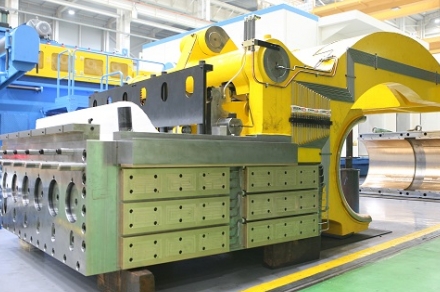
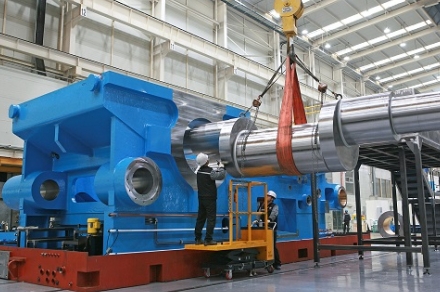
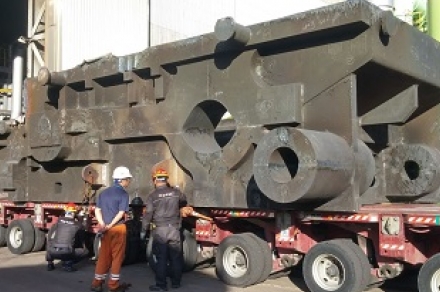

Provided by Hyodong,
recompiled by Dean Tseng, Fastener World
Hyodong Machine manufactures cold forging machines designed to produce nuts, bolts and all essential parts needed in industry fields such as automotive, electronics, construction and energy. Hyodong was founded in 1983 to produce rolling machines, pointing machines, heading machines and a variety of forging machines. In 1990, Hyodong developed a multistage former for the first time in the domestic forging industry which relied on expensive foreign machines. In 1993, Hyodong made a technical aid contract with Sakamura to combine advanced technology of both sides to become the best former maker in the industry occupying over 90% of the domestic market share. In the 21st century, Hyodong invests in the expansion of factory and high-tech facilities to produce better quality machines for customers.
Brace Yourself for the New Wonder of the Industry
On June 12, 2018, Hyodong announced the completion of the world’s first and largest former called “HBP-6220UL”, a six-station machine with a forging load of 2200 tons, cut-off diameter of 55 mm and cut-off length of 100 to 450mm. The machine’s punch size is Dia. 210 x 550 mm. The die sizes for stations one to four and station six are Dia. 280 x 550 mm, and Dia. 300 x 550 mm for station five. Its knock-out is 60 to 400 mm, PKO is 150 mm and ram stroke is 780 mm. The weight of the machine is 420 tons, which is twice as heavy as HBP-650.
The parts produced by HBP-6220UL in a pre-acceptance test were transmission shafts. In the past, the parts would have to be produced by a press or hot former, but now the arrival of HBP-6220UL has made it possible to produce with a cold former. The length of the parts is 410 mm and diameter of the flange is 115 mm. The parts were produced at a rate of 45 rpm in continuous production.
Static Pressure System & Top-Level Machine Structure
Hydraulic pressure of 18 kg/cm2 between the ram and liner is applied for optimum straightness, and this an option that guarantees concentricity of 0.03 mm. In addition, HBP-6220UL comes with the impact cutting system, slow jog system, air balance system, dead point elimination device, refeeding device and SPS system. The main body of HBP-6220UL is made of SC460 which is the best cast steel. The components have been cast, forged and machined by Doosan Heavy Industries & Construction which provides the most valuable casting technology in Korea.
The Nitty-Gritty
(1) Machine Frame—The total weight of the post-casting machine frame was 210 tons. After precise machining done on a five-face milling machine from Waldrich, which is the best large machine maker, the total weight was 185 tons.
(2) Main Gear—The main gear was fabricated in a forging process. Its weight was 75 tons after forging, and then became 19 tons after the inner and outer diameters were machined. Made as a double helical gear, it is manufactured to the highest quality and engineered to harness utmost power. Additionally, the gear is designed with a balanced structure to minimize the vibration of the machine.
Crank Shaft—Shape forging of 45 tons was completed for the crank shaft. The crank shaft produced with a cycle stroke of 780 mm had a 40 ton forging weight and a 32 ton weight after the work. The center diameter of the crank shaft is 900 mm.
Ram—Considering the tooling design for the test part’s characteristics (1500 ton forging load was needed at station five), the ram takes an asymmetrical design to obtain stability and prevent unbalanced loads (original station number one). Also, the static pressure system was adjusted to prevent excessive load on the ram liner due to unbalanced loads.
Hyodong Quality & International Recognition
To ensure reliable quality for customers, Hyodong makes around 80% of its formers’ components in its own manufacturing plant. Hyodong has the technology to manufacture customized machines for various customers and the biggest facilities. Its products are exported to many countries including Germany and Japan which means that its excellence of the quality is internationally recognized. Hyodong will keep developing technology to satisfy customers and become a maker of best quality machines in the world.
http://www.fastener-world.com.tw/hyodong