Industry Activities
BEST QUALITY WIRE Ultra S.S. Anti-Corrosion Screw- Rust-free for Over 30 Years & High Mechanical Properties Replacing Bi-metal Screws
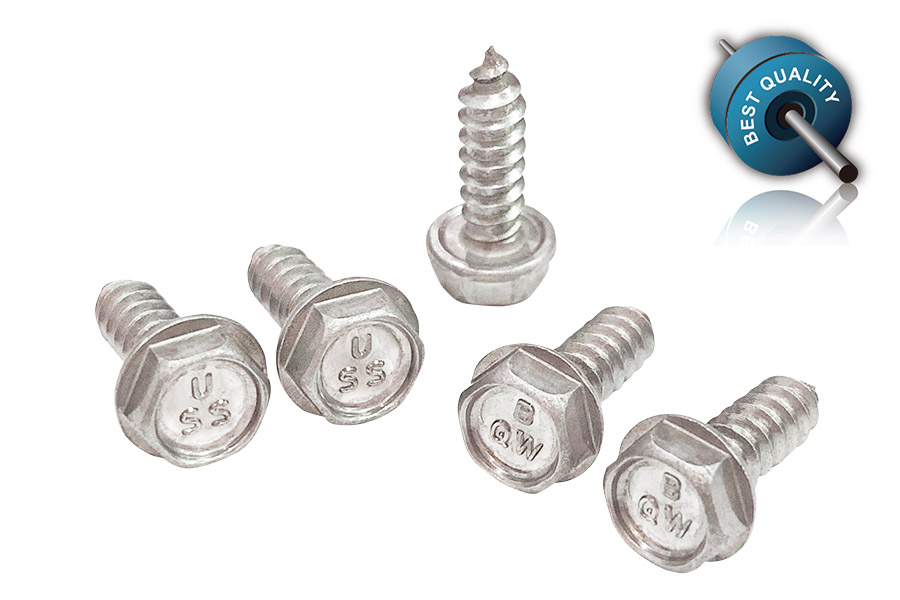

Add to my favorite
2024-11-20
Iconic Patent Fasteners Making a Reputation in Taiwan
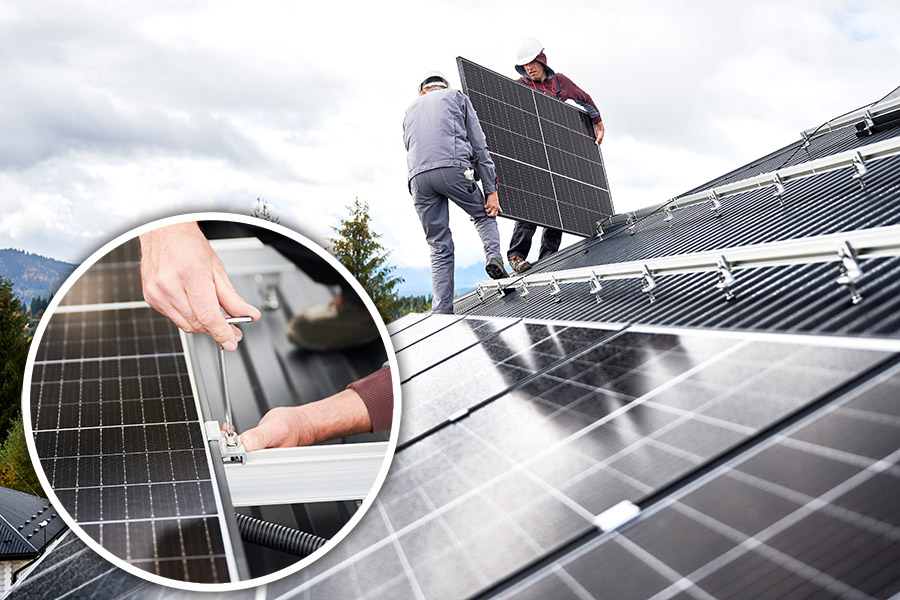
Best Quality Wire has crossed over from a wire rod company in Taiwan to the fastener R&D field, launching its flagship product, Ultra S.S. Anti-Corrosion Screw, with patents in Taiwan, Europe and the U.S. “Ultra S.S.” bears its own implication, representing apex stainless steel screw exceeding the properties of 304 and 316 stainless steel with exceptional rust resistance. Last year, it debuted at Taiwan International Fastener Show, garnering numerous inquiries and praise from domestic and international buyers.
This innovation came out of ten years of study and countless trials and errors by President Hsiang Wu. He discovered that bi-metal screw manufacturing involves multiple processes, resulting in lower production speed and volume compared to standard stainless steel screws. For many years, he contemplated how to address this issue and ultimately identified the pain point of bi-metal screws as the inability to form them in a single step. To solve it, he sought advice from industry experts and continuously studied process optimization and material characteristics, leading to the conception of a revolutionary new patent technology called Directly Drillable Stainless Steel Screw Forming Method. This technology is exclusive to Best Quality Wire, with no comparable alternatives on the market. The new product, Ultra S.S. Anti-Corrosion Screw, is a proud work adopting this technology.
Lower Costs, Shorter Delivery Times, Most Earth-Friendly
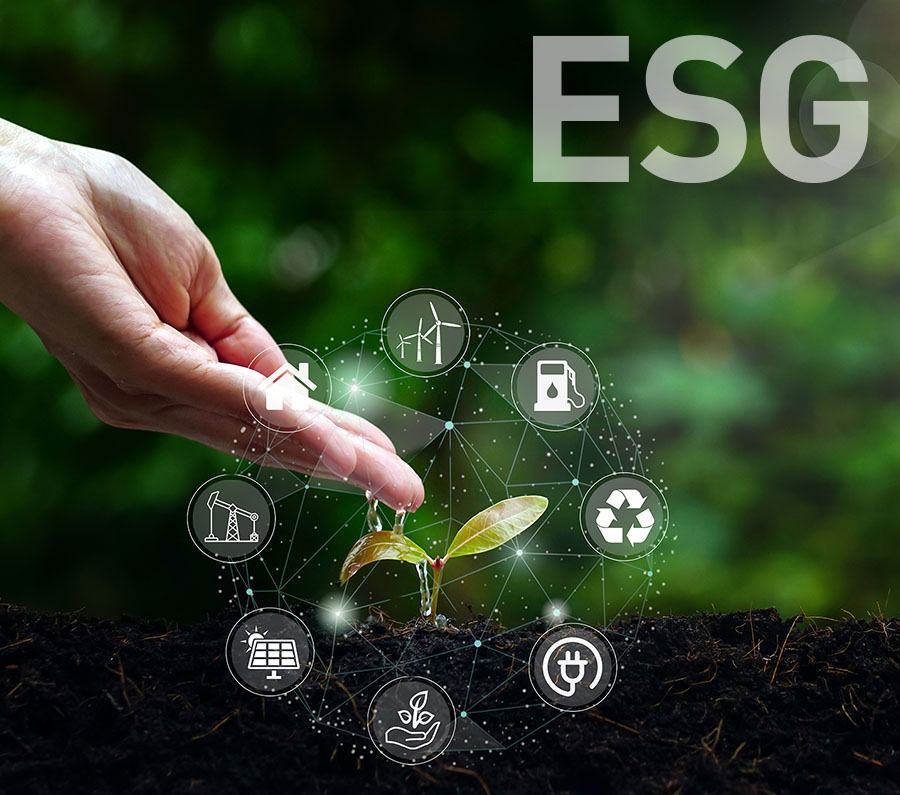
Before learning the advantages of this new product, it is essential to compare it with conventional bi-metal screw manufacturing processes. Typically, bi-metal screws consist of an upper structure made of stainless steel and a lower structure made of carbon steel. Since they have to combine dissimilar materials, the manufacturing process for bi-metal screws is complex and involves multiple steps. Additionally, it is difficult to keep the materials on the same center point during welding, leading to increased production costs and longer lead times. Furthermore, their corrosion resistance and strength are inferior, compounded by a more complex manufacturing process that has a larger environmental impact. This is the pain point of inability to form in a single step.
In contrast, Ultra S.S. Anti-Corrosion Screw addresses the issues by achieving single-step forming without processes like welding up two materials, machining, threading, cleaning, and surface treatment. It is formed in one step, resulting in faster production and shorter lead times. Consider that just eliminating those numerous steps can reduce labor, materials in use, factory space, time, and financial costs by up to 30-50% in a global inflationary environment—making its price competitiveness significant and highlighting its economic advantages! Moreover, it reduces carbon emissions during manufacturing by up to 20-40%, helping customers lower carbon tax costs while showcasing superior carbon reduction capabilities in international markets! With this product, Best Quality Wire has already optimized and shortened processes for customers beforehand, enhancing their market competitiveness. The benefits do not stop there. The President has invested considerable effort into studying material properties to make this product lighter with enhanced corrosion resistance and piercing strength.
Experimental results (Table 1) show its rust resistance surpasses that of 304 and 316 stainless steel. Its surface hardness reaches 550 HV, core hardness exceeds 520 HV, with a tensile strength of 173 kgf/cm2. It can withstand over 3,000 hours of corrosion and more than 30 cycles of acid rain exposure. Since it is inherently rust- and corrosion-resistant, no surface treatment is necessary. Ultimately, it can directly replace conventional bi-metal screws.
The President revealed to Fastener World: "The yacht, wind power, solar energy, construction, and automotive industries place high importance on strength and corrosion resistance—especially under marine conditions or harsh environments. I can guarantee that this screw will not rust for 20 to 30 years (Table 2), while its low-carbon manufacturing process significantly reduces environmental burdens. It can be widely used across these diverse industries while demonstrating consistent adaptability and corrosion resistance. In light of global inflation pressures combined with EU carbon taxes, it will undoubtedly help customers face challenges related to carbon taxes with greater cost competitiveness while contributing to environmental protection."
Table 1. Performance and Property Test Result
|
|||
Items
|
Ultra S.S. Anti-Corrosion Screw
|
Conventional Bi-metal Screws
|
SUS 410
|
Surface Hardness
|
550-650HV
|
210-250HV
|
561-578HV
|
Core Hardness
|
520-550HV
|
---
|
561-578HV
|
Tensile Strength
|
173 kgf/cm2
|
70.7 kgf/cm2
|
145-147 kgf/cm2
|
Corrosion Resistance
|
Over 3,000 hours
|
240-1,000 hours (after surface treatment)
|
Below 50 hours
|
Acid Rain Resistance
|
Over 30 cycles
|
---
|
Below 5 cycles
|
Table 2. Overall Evaluation of Corrosion & Acid Rain Resistance
|
|||
Screw Type
|
Corrosion Resistance
|
Salt Spray
Test Period
|
Notes
|
Ultra S.S. Anti-Corrosion Screw
|
High, suitable for marine and harsh environments
|
Over 3,000 hours
|
Exhibiting excellent long-term performance in corrosion resistance and fastening.
|
8.8 Grade Bolt
|
Medium, depending on surface treatment
|
Around 500 to 1,000 hours
|
Suitable for general environments, but requires regular maintenance to ensure its performance.
|
Stainless Steel 316
|
High, suitable for chemical processing and marine environments
|
1,000 to 2,000 hours
|
Performs well in chemical environments, but requires special attention in highly salty environments.
|
SCM435
|
Medium, should avoid high corrosion environments
|
200 to 500 hours
|
Poor corrosion resistance, not suitable for long-term use in humid environments.
|
A2-70
|
Medium, sensitive to highly salty environments
|
Around 300 hours
|
Applicable in normal environments, but may experience corrosion with long-term exposure to humid conditions.
|
"Single-step Forming" Technology Now Extends Application to Customized Assorted Fastener Development
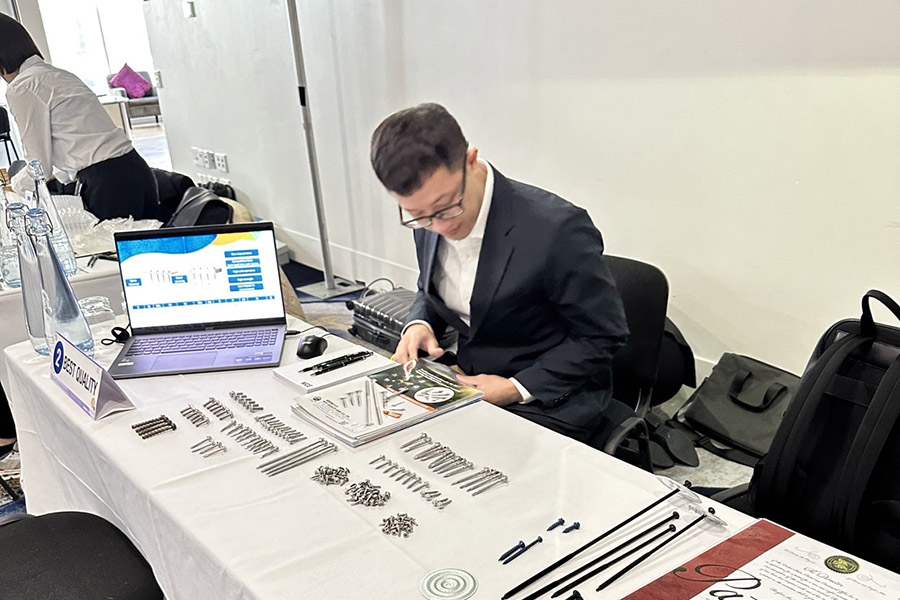
Having addressed the pain point of bi-metal screws, the President aims to extend this technology further into revolutionary optimization of wire rod manufacturing. He will develop a production line that incorporates wire drawing, pickling, roughing, finishing, and phosphoric acid coating into a single step. His production line will be able to produce wire rods in a single step with a major highlight of shortening processes and reducing carbon emissions. Furthermore, he will use this technology for customized production of nuts and various high-strength fasteners formed in a single step. Additionally, he commits to continuously contributing to ESG and has conducted carbon inventory. Best Quality Wire is fully equipped for the CBAM era!
Best Quality Wire’s contact: Mr. Hsiang Wu, President
Email: hsiang@bqw.com.tw
BEST QUALITY WIRE
Ultra S.S. Anti-Corrosion Screw
rust-free
high mechanical properties
replacement of bi-metal screw
Directly Drillable Stainless Steel Screw Forming Method
ESG
low carbon
wire Dusseldorf
FASTENER FAIR INDIA
FASTENER FAIR VIETNAM
FASTENER FAIR MEXICO
FASTENER POLAND
FASTENER FAIR ITALY
FASTENER FAIR GLOBAL
READ NEXT
Industry Activities
2024-11-20

Subscribe
