IOU GOOD JYI INDUSTRY CO., LTD.
About Company

IOU GOOD JYI INDUSTRY CO., LTD.

TAIWAN

NO.50, LANE 627, SEC.7, ERH SHI RD., ERH LIN, CHANGHUA COUNTY 52656, TAIWAN

886-4-868 4488

886-4-868 3899

Please login
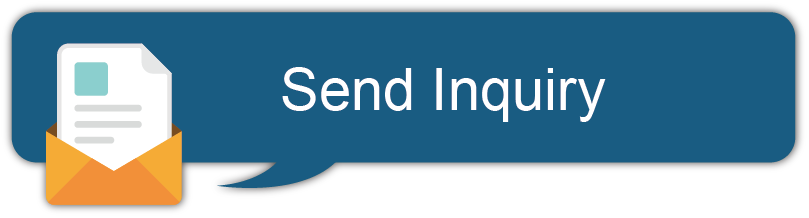

Model / Specification

Country of Origin
TAIWAN

Surface Treatment

Material

Alias

Patent

Head Marking

Capacity

Minimum Order Quantity

Detailed Description
"We fulfill what others can't."
Hard-to-cut Materials Draw the Line from Rivals
Fast forward back 40 years of corporate history. Iou Good Jyi mainly relied on table lathes and each person was in charge of one machine in the company’s early days. They earned just a meager profit from OEM, and saved every penny from it until it added up to a portion of funds with which they purchased the first automated lathe. The funds kept increasing until there were 10 lathes. That was a time of most intense competition, where they were in an industry in need of high craftsmanship. Everything from cam design to tool grinding and selection were all technical tasks. Back then, most Taiwanese competitors were just focused on processing easy-to-cut materials such as copper, aluminum, and free-cutting steel. In contrast, Iou Good Jyi was dedicated to difficult-to-cut materials like alloy steel, tool steel, stainless steel, and titanium alloys that others didn’t want to process, and that is what shaped the company’s manufacturing technique that stands out from the crowd. Now they supply precision hydraulic components as well as automobile, bicycle, optical, aerospace, medical parts and customized special parts. They manage and save costs for clients in the design phase, providing complete solutions on manufacturing methods as well as the most competitive prices.
Full Range of Machines to Meet Precision Requirements from Many Countries
Then came the automation and computerization trends that brought a different change to them. Customers were requiring higher precision which dictated the use of CNC machines. They purchased various machines with different functions, from Swiss Type CNC Lathe models 16, 20, 32 and 42 to CNC Turning Lathe models 25, 42, 52, etc., in order to meet various customers’ needs. Additionally, inspection equipment was added to the line, from horizontal projectors to vertical projectors, CNC 3D image measuring machines, surface roughness testers, roundness gauge, metallographic cutting machines, etc. They also introduced ISO 9001 certification in 2008 and had been widely praised by customers in satisfaction surveys over the years. Their products are sold across the world, such as EU, Japan, the U.S., and the Middle East.
"CNC Smart Manufacturing" and "Carbon Reduction",
Grasp the Big Trends of the Future
In response to high global awareness of energy conservation and carbon reduction, they have already implemented equipment for recycling and reusing oil, and most of their tools can be reground and reused. They also cooperate with clients to calculate carbon content of the manufacturing process as required in CBAM, and they reduce the carbon footprints from transportation of incoming materials. To contribute to the Earth, they have planted 500 trees since 2000 and continue to plant more.
The company has weathered several economic downturns since the establishment in 1984, each time inspiring their evolution towards better crisis management and preventive measures to ensure zero risk for clients. To efficiently achieve small-volume and diverse production, they introduced a flagship product by DP Technology, a smart manufacturing solution designed for CNC programming, process optimization and physical simulation. Looking ahead, with higher price and lack of materials as well as high personnel costs, the company will continue to transform into a smart green factory to join the future trend of carbon reduction and AI.
Hard-to-cut Materials Draw the Line from Rivals
Fast forward back 40 years of corporate history. Iou Good Jyi mainly relied on table lathes and each person was in charge of one machine in the company’s early days. They earned just a meager profit from OEM, and saved every penny from it until it added up to a portion of funds with which they purchased the first automated lathe. The funds kept increasing until there were 10 lathes. That was a time of most intense competition, where they were in an industry in need of high craftsmanship. Everything from cam design to tool grinding and selection were all technical tasks. Back then, most Taiwanese competitors were just focused on processing easy-to-cut materials such as copper, aluminum, and free-cutting steel. In contrast, Iou Good Jyi was dedicated to difficult-to-cut materials like alloy steel, tool steel, stainless steel, and titanium alloys that others didn’t want to process, and that is what shaped the company’s manufacturing technique that stands out from the crowd. Now they supply precision hydraulic components as well as automobile, bicycle, optical, aerospace, medical parts and customized special parts. They manage and save costs for clients in the design phase, providing complete solutions on manufacturing methods as well as the most competitive prices.
Full Range of Machines to Meet Precision Requirements from Many Countries
Then came the automation and computerization trends that brought a different change to them. Customers were requiring higher precision which dictated the use of CNC machines. They purchased various machines with different functions, from Swiss Type CNC Lathe models 16, 20, 32 and 42 to CNC Turning Lathe models 25, 42, 52, etc., in order to meet various customers’ needs. Additionally, inspection equipment was added to the line, from horizontal projectors to vertical projectors, CNC 3D image measuring machines, surface roughness testers, roundness gauge, metallographic cutting machines, etc. They also introduced ISO 9001 certification in 2008 and had been widely praised by customers in satisfaction surveys over the years. Their products are sold across the world, such as EU, Japan, the U.S., and the Middle East.
"CNC Smart Manufacturing" and "Carbon Reduction",
Grasp the Big Trends of the Future
In response to high global awareness of energy conservation and carbon reduction, they have already implemented equipment for recycling and reusing oil, and most of their tools can be reground and reused. They also cooperate with clients to calculate carbon content of the manufacturing process as required in CBAM, and they reduce the carbon footprints from transportation of incoming materials. To contribute to the Earth, they have planted 500 trees since 2000 and continue to plant more.
The company has weathered several economic downturns since the establishment in 1984, each time inspiring their evolution towards better crisis management and preventive measures to ensure zero risk for clients. To efficiently achieve small-volume and diverse production, they introduced a flagship product by DP Technology, a smart manufacturing solution designed for CNC programming, process optimization and physical simulation. Looking ahead, with higher price and lack of materials as well as high personnel costs, the company will continue to transform into a smart green factory to join the future trend of carbon reduction and AI.
Message Board