News
Japanese Yamahiro Adopts Co-developed IoT System
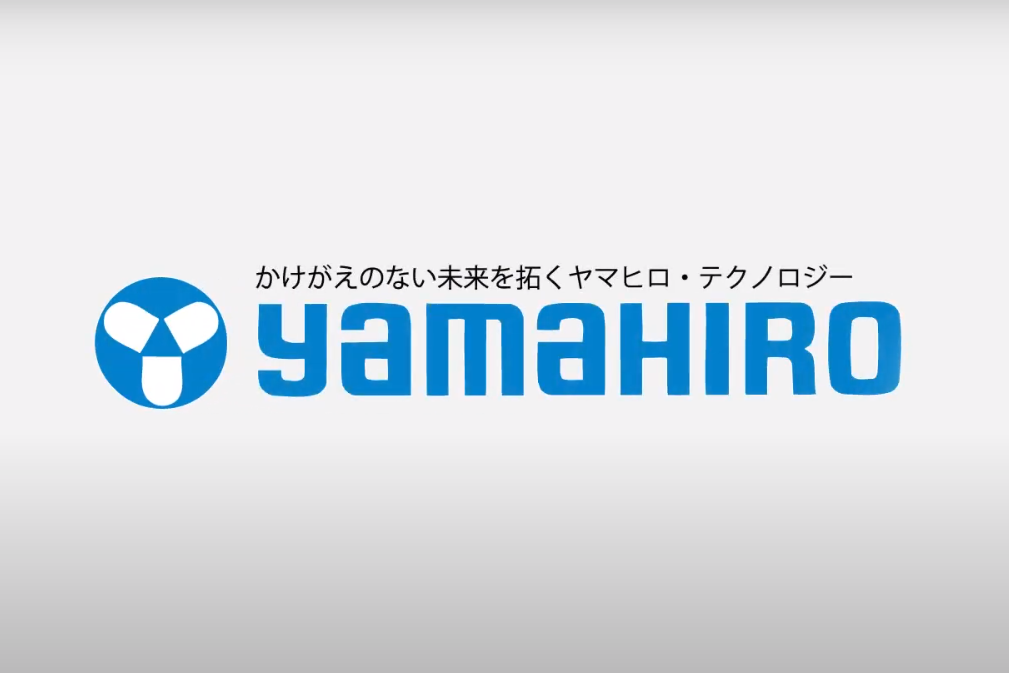

Add to my favorite
2022-03-29
Yamahiro is a construction fastener manufacturer and developer headquartered in Osaka. The company decided to introduce an IoT system to improve productivity. The practical experience they shared can shed a light on the efficacy from upgrading to smart factory and the tasks to heed.
At first they purchased an IoT system worth a million Japanese dollars and tried connecting it to 3 machines, but they were not able to get the specific data they wanted. They thought they have their own technical people, so they headed on to co-develop their own IoT system. They had the technical personnel collect data from machines, and had another person use the Amazon Web Services platform (a cloud-computing platform established by Amazon).
Using IoT, the first change they observed is the ability to measure productivity. By "visualizing data", they discovered they had less than 50% of total machine utilization. Knowing why and for how long the machines had stopped, they were able to improve to 85% and increase productivity by 170%. They used to have 2 shifts till 9 pm. Now they can achieve the same level of productivity on just the 1st shift till 5 pm. Besides shortening work time, they saved electricity bills, shortened 30 minutes from taking inventory, and discovered other unforeseen problems.
The second change is "data sharing". Everyone including the employees and owner with a computer can see the data and give suggestions on the spot. If the owner sees a machine not operating, he will give orders to onsite personnel right away. Therefore, they solved the bottleneck in the fastener heading process.
The third change is "prolonging dies life". They started with dies requiring frequent change, and were able to go from one hour a time to ten hours a time for changing the dies, saving work time.
Right now their most critical task is to cultivate analytic talents. It is very time-consuming to analyze data and therefore requires experienced people to take charge. The other task is to reduce errors by onsite personnel who collect and input machine data which also requires management by a dedicated person. Their next step is to apply IoT to threading, forming and packaging to save labor and freights, through which they can form a distribution unit in the company to maintain profit margin and tackle the challenges from the pandemic. The workforce saved from the production line can be assigned to the work with higher added values.
At first they purchased an IoT system worth a million Japanese dollars and tried connecting it to 3 machines, but they were not able to get the specific data they wanted. They thought they have their own technical people, so they headed on to co-develop their own IoT system. They had the technical personnel collect data from machines, and had another person use the Amazon Web Services platform (a cloud-computing platform established by Amazon).
Using IoT, the first change they observed is the ability to measure productivity. By "visualizing data", they discovered they had less than 50% of total machine utilization. Knowing why and for how long the machines had stopped, they were able to improve to 85% and increase productivity by 170%. They used to have 2 shifts till 9 pm. Now they can achieve the same level of productivity on just the 1st shift till 5 pm. Besides shortening work time, they saved electricity bills, shortened 30 minutes from taking inventory, and discovered other unforeseen problems.
The second change is "data sharing". Everyone including the employees and owner with a computer can see the data and give suggestions on the spot. If the owner sees a machine not operating, he will give orders to onsite personnel right away. Therefore, they solved the bottleneck in the fastener heading process.
The third change is "prolonging dies life". They started with dies requiring frequent change, and were able to go from one hour a time to ten hours a time for changing the dies, saving work time.
Right now their most critical task is to cultivate analytic talents. It is very time-consuming to analyze data and therefore requires experienced people to take charge. The other task is to reduce errors by onsite personnel who collect and input machine data which also requires management by a dedicated person. Their next step is to apply IoT to threading, forming and packaging to save labor and freights, through which they can form a distribution unit in the company to maintain profit margin and tackle the challenges from the pandemic. The workforce saved from the production line can be assigned to the work with higher added values.
Yamahiro
物聯網
IoT system
生產力
productivity
數據共有化
data sharing
延長模具壽命
prolonging dies life
扣件
國際展會
惠達雜誌
匯達實業
外銷媒合
廣告刊登
螺絲五金
五金工具
紧固件
台灣扣件展
印度新德里螺絲展
越南河內螺絲展
墨西哥瓜達拉哈拉螺絲展
美國拉斯維加斯螺絲暨機械設備展
波蘭克拉科夫螺絲展
義大利米蘭螺絲展
德國司徒加特螺絲展
wire Dusseldorf
FASTENER FAIR INDIA
FASTENER FAIR VIETNAM
FASTENER FAIR MEXICO
FASTENER POLAND
FASTENER FAIR ITALY
FASTENER FAIR GLOBAL
FASTENER WORLD
READ NEXT

Subscribe
